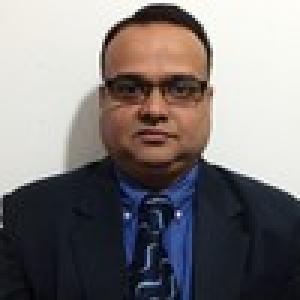
$$$$
{{ $t($store.state.user.experience_value_in_dollars) }}
Expert
{{ $t($store.state.user.experience_search_name) }}
0
jobs
Lean / Continuous Improvement Consultant ( Toyota Production System)
Makarand Kulkarni
,
Aylesbury, United Kingdom
Experience
Other titles
Skills
I'm offering
A Chemical Engineering graduate with over 25 year's experience in Project Management, Operations, Lean Consultancy and Continuous Improvement (CI) leadership roles. Have worked with several blue chip organisations like Unilever, BASF, Thermo Fisher,Kerry Foods ,2 Sisters Food Group,plaids,UK http://*****.** the FMCG manufacturing sector. Fully versed in Lean Six Sigma tools and techniques (Toyota Production System, Total Productive Maintenance-JIPM, Value Stream Mapping,8 Step Problem Solving,5S,Standard Work & SOP ,Visual Management, Task Mapping, Process Mapping, Gemba Walk, Root Cause Counter Measure,OEE ,etc) and Lean Systems Certification from University of Kentucky, USA (comparable with Lean Six Sigma Master Black Belt)
Markets
United States
United Kingdom
France
Germany
Lithuania
Denmark
Norway
Sweden
Finland
Links for more
Once you have created a company account and a job, you can access the profiles links.
Language
English
Fluently
Ready for
Larger project
Ongoing relation / part-time
Full time contractor
Available
My experience
2018 - ?
freelance
Continuous Improvement / Lean Consultant
U-Pol Ltd.
- Automotive Refinishing Products Manufacturer, United Kingdom (March 2018 till date) Continuous Improvement / Lean Consultant (Director - MAKLEAN CONSULTING LTD.)
• Currently Supporting the Wellingborough Site as C I/ Lean Consultant by:
Help developing the Improvement Plans across all departments including C I Improvement Plan (£550K Identified and £450K Planned for 2020)
• Help improving the Tier Accountability Process. Reduced the meeting time by 70% at middle / Senior management level meeting.
• Help Improving OEE by 22% on newly installed automated filling line as a part of transformation project.
• Delivering Kaizen Events involving cross functional teams and using 8 Step Problem Solving process across the site (21 nos. planned, and 21 nos. delivered in 2019.24 nos. Planned in 2020 & 2 nos. delivered so far)
• Delivering OEE Awareness & 5S Training to Front line, Middle and Senior Managers.
• Supporting Capex Projects across the site.
• Conducting Time and Motion Studies, OEE analysis, Process Mapping, Root Cause Analysis , 8 Step Problem Solving, Line Balancing ,Standardizing Machine Settings for more than 100's of SKU's, reviewing SOP's etc. to improve the labour productivity and reduce the downtime on focused filling lines and in manufacturing areas.
• Preparing and Presenting the transformation project improvements to the Chairman, CEO, Board of Directors etc.
• Currently Supporting the Wellingborough Site as C I/ Lean Consultant by:
Help developing the Improvement Plans across all departments including C I Improvement Plan (£550K Identified and £450K Planned for 2020)
• Help improving the Tier Accountability Process. Reduced the meeting time by 70% at middle / Senior management level meeting.
• Help Improving OEE by 22% on newly installed automated filling line as a part of transformation project.
• Delivering Kaizen Events involving cross functional teams and using 8 Step Problem Solving process across the site (21 nos. planned, and 21 nos. delivered in 2019.24 nos. Planned in 2020 & 2 nos. delivered so far)
• Delivering OEE Awareness & 5S Training to Front line, Middle and Senior Managers.
• Supporting Capex Projects across the site.
• Conducting Time and Motion Studies, OEE analysis, Process Mapping, Root Cause Analysis , 8 Step Problem Solving, Line Balancing ,Standardizing Machine Settings for more than 100's of SKU's, reviewing SOP's etc. to improve the labour productivity and reduce the downtime on focused filling lines and in manufacturing areas.
• Preparing and Presenting the transformation project improvements to the Chairman, CEO, Board of Directors etc.
Training, C, Lean, Continuous improvement, Consulting, Management, Transformation, Process Mapping, Presenting, Ceo, Kaizen
2017 - 2018
job
Regional Excellence Implementation Manager -Southern (UK & Europe Cluster)
Pladis (McVities, Godiva, Ulker).
Major Achievements (Across 5 Manufacturing Sites of responsibility):
• Delivered £2.1m productivity savings across five sites (Manchester, Liverpool -Aintree, Leicester -Wigston, Halifax and London - Harlesden).Lead the Diagnostic Loss Reduction Project - the journey to zero.and helped sites developing the 2018 pipeline to deliver £2.5m savings across all sites in the UK.
• Implemented Loss Analysis, Waste Mapping, OEE Analysis, Process Mapping, Value stream Mapping, Speedy Kaizen (less than one day), Factor Tree Analysis, Focused Breakthrough Improvement (FBI) Activities (6-8 weeks) One Piece Flow to develop the pipeline to deliver the productivity savings. Tier Accountability Process (Tier 1, 2, 3 & 4) to sustain the standards. Dynamic Standard Operating Procedures, Leader Standard Work (Gemba Walk), Process Confirmation, Tactical Implementation Plan (TIP 1- Short Term and Tip 0 - Long Term)
• Conducted the site maturity assessment to improve the maturity level from Phase 0 to Phase 1 across five sites.
• Lead the loss reduction project and developing the diagnostic approach (Blueprint) to identify end to end losses on the production lines /services reduce those using Focused Improvement (Problem Solving) Tools and sustain using Leadership Tools (behaviors).
• Delivered £2.1m productivity savings across five sites (Manchester, Liverpool -Aintree, Leicester -Wigston, Halifax and London - Harlesden).Lead the Diagnostic Loss Reduction Project - the journey to zero.and helped sites developing the 2018 pipeline to deliver £2.5m savings across all sites in the UK.
• Implemented Loss Analysis, Waste Mapping, OEE Analysis, Process Mapping, Value stream Mapping, Speedy Kaizen (less than one day), Factor Tree Analysis, Focused Breakthrough Improvement (FBI) Activities (6-8 weeks) One Piece Flow to develop the pipeline to deliver the productivity savings. Tier Accountability Process (Tier 1, 2, 3 & 4) to sustain the standards. Dynamic Standard Operating Procedures, Leader Standard Work (Gemba Walk), Process Confirmation, Tactical Implementation Plan (TIP 1- Short Term and Tip 0 - Long Term)
• Conducted the site maturity assessment to improve the maturity level from Phase 0 to Phase 1 across five sites.
• Lead the loss reduction project and developing the diagnostic approach (Blueprint) to identify end to end losses on the production lines /services reduce those using Focused Improvement (Problem Solving) Tools and sustain using Leadership Tools (behaviors).
Leadership, Less, Implementation, Process Mapping, Assessment, Value stream mapping, Production, Kaizen, Manager
2015 - 2017
job
PPI Business Systems Manager - Europe Microbiology Division (Regional C I Manager)
Thermo fisher Scientific.
(August 2015 to May 2017)
PPI Business Systems Manager - Europe Microbiology Division (Regional C I Manager)
Major Achievements (Across 6 manufacturing sites in UK, Germany & Finland of responsibility):
Productivity Savings:
• Delivered $763K productivity savings in 2015 at Basingstoke Site (370 employees).
• Delivered $1.92m productivity savings at Basingstoke Site against $1.26m Target for 2016.
• Developed the robust productivity pipeline for next three years (over $5.0m for 2017-19) through Value Stream Mapping, KPI Gap Analysis, Daily Tier Meetings, and Financial Review with each functional head etc.
• Trained more than 85% (of 370 employees) in 8 Steps at Basingstoke Site.
• Qualified as (8 Step) Process Manager in less than four months of joining the business.
• Identified and qualified 9 Process Managers across 6 sites in Europe.
• Developed and implemented Lean Conversion Plan including tools like Value Stream Mapping, 5'S, Standard Work & SOP, Gemba Card - Process Confirmation, 8 Step Problem Solving and Root Cause Counter Measure, Leader Standard Work, OEE etc. in the Model Area identified by the team at Basingstoke.
• Conducted the site maturity assessment and improved the assessment score from 2.5 to 3.0 at Basingstoke Site (Maximum achievable is 5.0 in each category) in 2016.
• Planned and conducted "Kaizen Institute" - a weeklong kaizen (Global) event to deliver 3 projects at Basingstoke.
• Developed and delivered PFMEA (Process Failure Mode Effects Analysis) in Cartridges area at Basingstoke.
• Facilitated and delivered 24 kaizen events, 61 Just Do It's and 8 nos. 8 Step Classic events.
PPI Business Systems Manager - Europe Microbiology Division (Regional C I Manager)
Major Achievements (Across 6 manufacturing sites in UK, Germany & Finland of responsibility):
Productivity Savings:
• Delivered $763K productivity savings in 2015 at Basingstoke Site (370 employees).
• Delivered $1.92m productivity savings at Basingstoke Site against $1.26m Target for 2016.
• Developed the robust productivity pipeline for next three years (over $5.0m for 2017-19) through Value Stream Mapping, KPI Gap Analysis, Daily Tier Meetings, and Financial Review with each functional head etc.
• Trained more than 85% (of 370 employees) in 8 Steps at Basingstoke Site.
• Qualified as (8 Step) Process Manager in less than four months of joining the business.
• Identified and qualified 9 Process Managers across 6 sites in Europe.
• Developed and implemented Lean Conversion Plan including tools like Value Stream Mapping, 5'S, Standard Work & SOP, Gemba Card - Process Confirmation, 8 Step Problem Solving and Root Cause Counter Measure, Leader Standard Work, OEE etc. in the Model Area identified by the team at Basingstoke.
• Conducted the site maturity assessment and improved the assessment score from 2.5 to 3.0 at Basingstoke Site (Maximum achievable is 5.0 in each category) in 2016.
• Planned and conducted "Kaizen Institute" - a weeklong kaizen (Global) event to deliver 3 projects at Basingstoke.
• Developed and delivered PFMEA (Process Failure Mode Effects Analysis) in Cartridges area at Basingstoke.
• Facilitated and delivered 24 kaizen events, 61 Just Do It's and 8 nos. 8 Step Classic events.
C, Lean, Event, Less, It, KPI, Mode, Assessment, Value stream mapping, Kaizen, Manager
2014 - 2015
job
Divisional Manufacturing Excellence Manager
Sisters Food Group.
Added Value Poultry Division (1700 Employees)
Major Achievements (Across 4 Added Value Poultry Sites in the UK):
• Developed the AVP Divisional Strategy and Lean Deployment Model across 4 AV Poultry Sites.
• Achieved M&S Plan A Silver Validation for Thetford Site and developed the Master Plan for Gold.
• Recruited and developed Manufacturing Excellence Team at Cambuslang and Five Star Fish Sites.
• Developed & implemented the "One Way of Working - Manufacturing Excellence Model based on Lean Six Sigma" (Balanced Scorecard, Tier Process, Line Configuration Sheets, Short Interval Control Board, and Problem Solving & Process Confirmation) at Cambuslang Site in Scotland.
• Helped delivering positive KPI's at Cambuslang Site resulting in profit of £250k/week from loss of £350k/week before the lean deployment.
• Deployed Economic Framework (Lean) for M&S Plan A Silver at Cambuslang and Five Star Fish Sites.
• Carried out KPI Gap Analysis with Site GM's this has identified £ 6.6m opportunity across 3 sites.
• Developed and delivered presentations at Divisional Meetings.
Major Achievements (Across 4 Added Value Poultry Sites in the UK):
• Developed the AVP Divisional Strategy and Lean Deployment Model across 4 AV Poultry Sites.
• Achieved M&S Plan A Silver Validation for Thetford Site and developed the Master Plan for Gold.
• Recruited and developed Manufacturing Excellence Team at Cambuslang and Five Star Fish Sites.
• Developed & implemented the "One Way of Working - Manufacturing Excellence Model based on Lean Six Sigma" (Balanced Scorecard, Tier Process, Line Configuration Sheets, Short Interval Control Board, and Problem Solving & Process Confirmation) at Cambuslang Site in Scotland.
• Helped delivering positive KPI's at Cambuslang Site resulting in profit of £250k/week from loss of £350k/week before the lean deployment.
• Deployed Economic Framework (Lean) for M&S Plan A Silver at Cambuslang and Five Star Fish Sites.
• Carried out KPI Gap Analysis with Site GM's this has identified £ 6.6m opportunity across 3 sites.
• Developed and delivered presentations at Divisional Meetings.
Deployment, Lean, Six Sigma, KPI, Framework, Sigma, Manager
2010 - 2014
job
Unit Lean Co-Ordinator - Windmill Lane Site
Kerry Foods.
(850 Employees)
Major Achievements:
• Developed & implemented the Site KPS Strategy with the help of Regional KPS Technology Lead to change the culture from "Who" to "Why" which has enabled the Site Teams finding the problem, fixing the problem & keep the problem from coming back.
• Developed C I Managers (3nos.), KPS Coaches (6nos.), Training Co-coordinators (5nos.) and 8 Step Mentors (13 nos.) including Front Line, Middle and Senior Managers across the Site.
• Delivered £1.56 Million savings by site teams delivering prioritized projects,identified through Opportunity Assessment on Labour, Waste, Automation, Inventory Reduction etc. over three years from 2011 at Windmill Lane Site.
• Implemented five out of Six KPS Stabilisation elements i.e. Master Schedule, Practical Problem solving (8 Step PPS), Standard Work Element Sheets & Standard Operating Procedure, Visual Management (ATP, PFU etc.) and Layered Confirmation in Packing, Cartooning, Warehouse, and Dispatch & Kitchen at Windmill Lane Site.
• Achieved Jishuken Level 3 (2011); Jishuken Level 4 (2012) and Jishuken Level 5 (2014) during Kerry Production System Maturity Assessment by Kerry Food's Lean Specialist Coach.
• The Windmill Lane Site has received "Service Level" and" Customer (Sainsbury's) Excellence Award" through Continuous Improvement.
Major Achievements:
• Developed & implemented the Site KPS Strategy with the help of Regional KPS Technology Lead to change the culture from "Who" to "Why" which has enabled the Site Teams finding the problem, fixing the problem & keep the problem from coming back.
• Developed C I Managers (3nos.), KPS Coaches (6nos.), Training Co-coordinators (5nos.) and 8 Step Mentors (13 nos.) including Front Line, Middle and Senior Managers across the Site.
• Delivered £1.56 Million savings by site teams delivering prioritized projects,identified through Opportunity Assessment on Labour, Waste, Automation, Inventory Reduction etc. over three years from 2011 at Windmill Lane Site.
• Implemented five out of Six KPS Stabilisation elements i.e. Master Schedule, Practical Problem solving (8 Step PPS), Standard Work Element Sheets & Standard Operating Procedure, Visual Management (ATP, PFU etc.) and Layered Confirmation in Packing, Cartooning, Warehouse, and Dispatch & Kitchen at Windmill Lane Site.
• Achieved Jishuken Level 3 (2011); Jishuken Level 4 (2012) and Jishuken Level 5 (2014) during Kerry Production System Maturity Assessment by Kerry Food's Lean Specialist Coach.
• The Windmill Lane Site has received "Service Level" and" Customer (Sainsbury's) Excellence Award" through Continuous Improvement.
Training, Automation, C, Lean, Continuous improvement, Management, Service, Technology, Coach, Assessment, Production
2009 - 2010
freelance
Lean Six Sigma Consultant
Penmark Ltd.
(Contractor)
Major Achievements:
• Successfully implemented "Meet & Greet" project for Ringways at Kent Highway Services.
• Identified the root cause of "Vehicle Returns" to depot by Interviewing the staff & drivers. Also, by using Fishbone (Cause & Effect) analysis.
• Identified the opportunities for Process & Service mapping during the project.
• Reduced defects cost by 50% for safety critical minor work like pothole repair etc.
• Reduced no. of gangs by 40 % in four weeks' project at Kent Highways. This would deliver £1.9m savings year on year basis.
• Improved the Gang Productivity from 4.6 jobs to 7.7 jobs / gang / day in four weeks.
• Positive effect on Team involved from Ringway as well as Kent Highway Services.
• 61 % reduction in backlogs was achieved by effective forward hub planning.
• Trained the Hub Team for effective utilization of Vehicle Tracking System like Masternaut.
• Trained the Hub Team for data analysis and presentation to Ringway and Kent County Council Senior Management.
• Captured Failure Modes across the county and identified opportunities for improvement.
• Designed Failure Cards and written Standard Operating Procedure for failure capturing and analysis. Trained alliance team for failure modes capturing & analysis.
• The work was well appreciated by Penmark as well as Ringway.
• Ringway awarded the third phase project to Penmark.
Major Achievements:
• Successfully implemented "Meet & Greet" project for Ringways at Kent Highway Services.
• Identified the root cause of "Vehicle Returns" to depot by Interviewing the staff & drivers. Also, by using Fishbone (Cause & Effect) analysis.
• Identified the opportunities for Process & Service mapping during the project.
• Reduced defects cost by 50% for safety critical minor work like pothole repair etc.
• Reduced no. of gangs by 40 % in four weeks' project at Kent Highways. This would deliver £1.9m savings year on year basis.
• Improved the Gang Productivity from 4.6 jobs to 7.7 jobs / gang / day in four weeks.
• Positive effect on Team involved from Ringway as well as Kent Highway Services.
• 61 % reduction in backlogs was achieved by effective forward hub planning.
• Trained the Hub Team for effective utilization of Vehicle Tracking System like Masternaut.
• Trained the Hub Team for data analysis and presentation to Ringway and Kent County Council Senior Management.
• Captured Failure Modes across the county and identified opportunities for improvement.
• Designed Failure Cards and written Standard Operating Procedure for failure capturing and analysis. Trained alliance team for failure modes capturing & analysis.
• The work was well appreciated by Penmark as well as Ringway.
• Ringway awarded the third phase project to Penmark.
Data Analysis, Lean, Management, Service, Six Sigma, Safety, Sigma
2004 - 2008
job
Factory Manager
Ocean Soaps Ltd.
Major Projects & Achievements:
• Developed the teams at Line Leader, Supervisor & Managers Level.
• Prepared for Fiji Business Excellence Award based on Australian Framework Standards - Achievement & Prize Level and received the achievement level in 2005 & Prize Level in 2006.
• Implemented Kaizen Technique for productivity improvement in Ocean Soaps.
• Launched 5'S program along with Training & Productivity Authority of Fiji (TPAF) in March 2006 to promote Ocean Soaps as 5'S Model organization as declared by TPAF.
• Selected & Attended Demonstration project (5'S) Workshop by Asian productivity organization, Japan in Phnom Penh, Cambodia from 10-13th December '07.
• Completed Training of Trainers Module I course by Training & Productivity Authority of Fiji. Also, undergone the Assessment for Training Instructor II & became Certified Training Instructor II in March 2007. Also, completed Training of Trainers Module II in May 2008.
• Developed the teams at Line Leader, Supervisor & Managers Level.
• Prepared for Fiji Business Excellence Award based on Australian Framework Standards - Achievement & Prize Level and received the achievement level in 2005 & Prize Level in 2006.
• Implemented Kaizen Technique for productivity improvement in Ocean Soaps.
• Launched 5'S program along with Training & Productivity Authority of Fiji (TPAF) in March 2006 to promote Ocean Soaps as 5'S Model organization as declared by TPAF.
• Selected & Attended Demonstration project (5'S) Workshop by Asian productivity organization, Japan in Phnom Penh, Cambodia from 10-13th December '07.
• Completed Training of Trainers Module I course by Training & Productivity Authority of Fiji. Also, undergone the Assessment for Training Instructor II & became Certified Training Instructor II in March 2007. Also, completed Training of Trainers Module II in May 2008.
Training, Business excellence, Assessment, Workshop, Kaizen, Framework, Manager
2001 - 2004
job
Production Officer (All India Grade)
Hindustan Unilever Ltd.
Major Projects & Achievements:
• Handled the shift operations, no. of people reporting = 54 nos.(Two Union INTUC & HLL) Achieved 100% Production Plan Compliance. Achieved highest production in bars (65,000MT/Annum) & powders (35,000 MT/Annum), reduced one headcount each in Bars & Powders Production setup.
• Implemented Total Productive Maintenance (TPM) methodology for Powders weight control and achieved TPM LEVEL 1 Award by JIPM (Japanese Institute of Planned Maintenance). Worked as a CIRCLE LEADER. Shift Circle has achieved BEST CIRCLE AWARD for JAN - MAR' 03 Quarter.
• Achieved Rs. 1.92 Crores (£192K) Technical Efficiency Savings against Rs.1.75 Crores (£175K) target for year 2001 by resolving process issues.
• Implemented auto batching in detergent bar & detergent powder manufacturing using PLC. Achieved Highest Production in Powders among three shifts. Reduced 03 people per shift.
• Worked as Member of Bars and Powders HACCP (hazard Analysis and Critical Control Point); UQCSRM (Unilever Quality Cost and Safety Road Map); Cost reduction and TPM Team.
• Handled the shift operations, no. of people reporting = 54 nos.(Two Union INTUC & HLL) Achieved 100% Production Plan Compliance. Achieved highest production in bars (65,000MT/Annum) & powders (35,000 MT/Annum), reduced one headcount each in Bars & Powders Production setup.
• Implemented Total Productive Maintenance (TPM) methodology for Powders weight control and achieved TPM LEVEL 1 Award by JIPM (Japanese Institute of Planned Maintenance). Worked as a CIRCLE LEADER. Shift Circle has achieved BEST CIRCLE AWARD for JAN - MAR' 03 Quarter.
• Achieved Rs. 1.92 Crores (£192K) Technical Efficiency Savings against Rs.1.75 Crores (£175K) target for year 2001 by resolving process issues.
• Implemented auto batching in detergent bar & detergent powder manufacturing using PLC. Achieved Highest Production in Powders among three shifts. Reduced 03 people per shift.
• Worked as Member of Bars and Powders HACCP (hazard Analysis and Critical Control Point); UQCSRM (Unilever Quality Cost and Safety Road Map); Cost reduction and TPM Team.
Operations, Compliance, PLC, Safety, HACCP, Production
1998 - 2001
job
Production Executive
Cyanamid Agro Ltd.
Major Projects & Achievements:
• Completed the Operational Readiness Review (ORR) must for plant start -up as per AHPC (American Home Products Corporation) Guidelines for production department.
• Written and implemented the Standard Operating Procedures for Durment 20 % E.C. (Chlorpyriphos) Abate 50 % EC (Temephos), Cythion 50% EC (Malathion), Stomp 30 % EC (Pendimethalin) and Pursuit 50 A (Imazythapur) formulations & achieved the production targets using PLC.
• Trained operators & management trainees for production.
• Selected as supporting member for Corporate Cost Reduction Team from plant.
• Completed the Operational Readiness Review (ORR) must for plant start -up as per AHPC (American Home Products Corporation) Guidelines for production department.
• Written and implemented the Standard Operating Procedures for Durment 20 % E.C. (Chlorpyriphos) Abate 50 % EC (Temephos), Cythion 50% EC (Malathion), Stomp 30 % EC (Pendimethalin) and Pursuit 50 A (Imazythapur) formulations & achieved the production targets using PLC.
• Trained operators & management trainees for production.
• Selected as supporting member for Corporate Cost Reduction Team from plant.
C, Management, PLC, Production, UP
1994 - 1998
job
Senior Officer - Projects
United Phosphorus Ltd.
Major projects & Achievements:
• Stood Four Times in organization TOP TEN KAIZEN competition.
• Worked as a Member of Safety Sub-Committee, Environment Management Cell and MIS Team. Exposure to Strategic Cost Reduction by Internal Team and Anderson Consulting (now Accenture).
• Stood Four Times in organization TOP TEN KAIZEN competition.
• Worked as a Member of Safety Sub-Committee, Environment Management Cell and MIS Team. Exposure to Strategic Cost Reduction by Internal Team and Anderson Consulting (now Accenture).
Consulting, Management, Safety, Kaizen
My education
2011
University of Kentucky
Lean Systems Certification, Toyota Production System
Lean Systems Certification, Toyota Production System
1989
-
1994
Shivaji University,India assessed by UKNARIC eqvt.to British Bachelor's Honours Degree
Bachelors of Engineering, Chemical
Bachelors of Engineering, Chemical
Makarand's reviews
Makarand has not received any reviews on Worksome.
Contact Makarand Kulkarni
Worksome removes the expensive intermediaries and gives you direct contact with relevant talent.
Create a login and get the opportunity to write to Makarand directly in Worksome.
are ready to help you
and get specific bids from skilled talent in Denmark